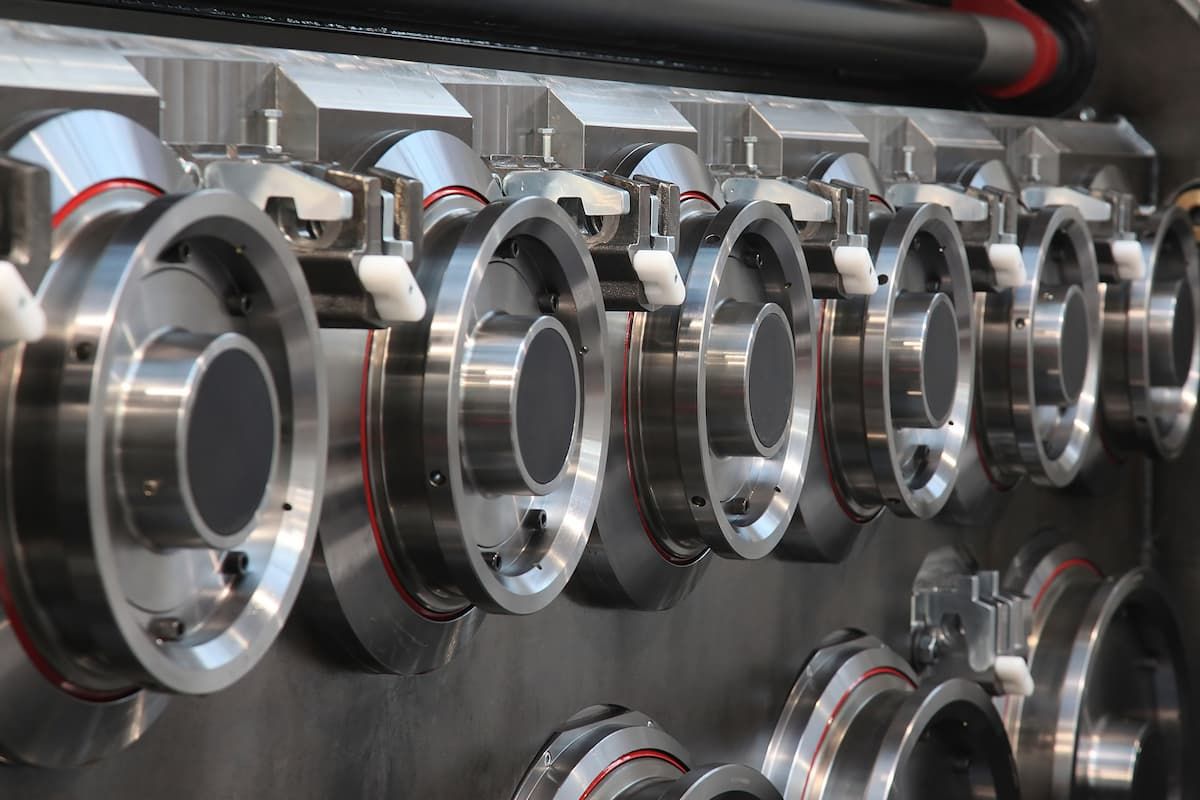
Maintenance of Wire Drawing Machines: Here’s Why It’s Important for Durability
In the field of metalworking, the maintenance of wire drawing machines is a crucial element to ensure efficiency, safety, and longevity of the machinery. This article, aimed at technicians and entrepreneurs, explores all aspects of maintenance for wire drawing machines. This article will discuss preventive maintenance and best practices.
The Role of Wear-Resistant and Ceramic Coatings
The wear-resistant or ceramic coating plays a vital role in protecting wire drawing machines. These coatings reduce friction, limit wear, and increase the machinery’s resistance to impacts and corrosion, thus ensuring greater durability and reducing the need for frequent maintenance.
In-depth Diagnostic Techniques and Tools
Timely diagnosis is essential to detect early signs of wear or malfunction, thus reducing the risk of sudden and costly breakdowns. Among these tools, vibration analyzers, thermal cameras, and sensor-based monitoring systems stand out, detecting anomalies in machinery performance.
For example, thermography is particularly effective in detecting points of excessive heat caused by friction or overload, while vibration analysis can indicate misalignments or imbalances in mechanical parts. Integrating these diagnostic tools into a preventive maintenance program allows for targeted interventions, reducing downtime and maintaining consistent production quality.
READ ALSO: Roller for Wear-Resistant Coatings: An Innovative Solution for Protection and Industrial Efficiency
Fundamental Steps for Maintenance
The maintenance of wire drawing machines involves various steps, including visual inspection, checking the proper functioning of all mechanical and electrical parts, and monitoring oil and other fluid levels. It is crucial to periodically replace components subject to wear, such as filters and seals, and ensure that all mechanical movements are smooth and unobstructed.
READ ALSO: Ceramic Drawing: Process, Advantages, and Innovations
Wear-Resistant Coatings in the Wire Drawing Sector
In the wire drawing sector, wear-resistant coatings play a fundamental role in prolonging the life of machines and maintaining their operational efficiency. These coatings are designed to protect the machine components from the stresses and abrasion caused by daily use.
The wire drawing process, which involves the deformation of metal through a series of dies, subjects the machines to intense and continuous mechanical stress. Without adequate protection, parts such as cylinders, rollers, pulleys, and gears can wear out quickly, reducing the precision of the process and increasing the frequency of maintenance interventions.
The wear-resistant coatings, such as those offered by Paganoni, are developed using advanced materials and innovative technologies to provide superior resistance to wear, heat, and corrosion. These coatings not only safeguard the metal parts by reducing friction and wear but also improve the sliding properties of the processed materials, contributing to optimizing the quality of the finished product.
Moreover, the adoption of wear-resistant coatings results in reduced operating costs, as the need to replace worn components occurs less frequently.
Turning to a specialized company like Paganoni means benefiting from consolidated experience, customized solutions adapted to the specific needs of each work context, and an approach that combines professionalism and proximity to the customer.