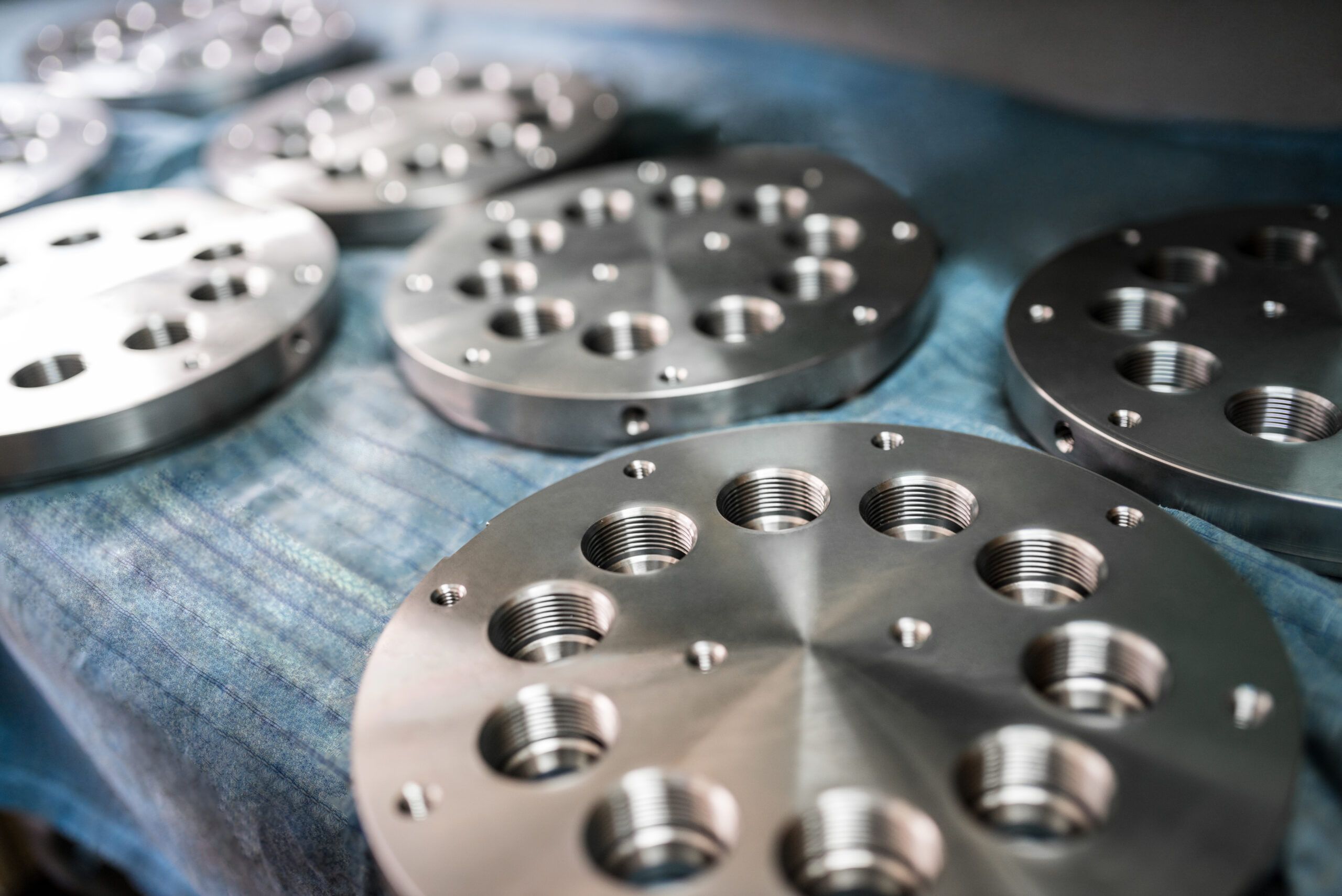
Evolution of drawing materials: from tungsten to chromium carbides
Industrial wire drawing is a key process in the production of wire used in a wide range of industries, from automotive to construction. Over time, the industry has constantly sought the best materials to protect the mechanical parts used in this critical process.
Let’s explore the evolution of materials for wear coatings used in wire drawing, with a focus on the transition from traditional tungsten coatings to the more modern chromium carbides.
The Tungsten Era
Since the 1970s, tungsten has dominated the field of wear coatings for industrial wire drawing. Tungsten coatings, such as Paganoni’s Wolside®, are known for their wear and impact resistance, making them ideal for protecting mechanical parts used in wire drawing mills. However, as technology advances and industry requirements increase, limitations related to corrosion and the complexity of the geometries to be coated have emerged.
Despite its advantages, tungsten has some significant disadvantages. For example, its vulnerability to corrosion in aggressive environments limits its performance in certain industrial applications. In addition, the complexity of the geometries to be coated can make it difficult for the coating application to be consistent, compromising the quality and durability of the mechanical part.
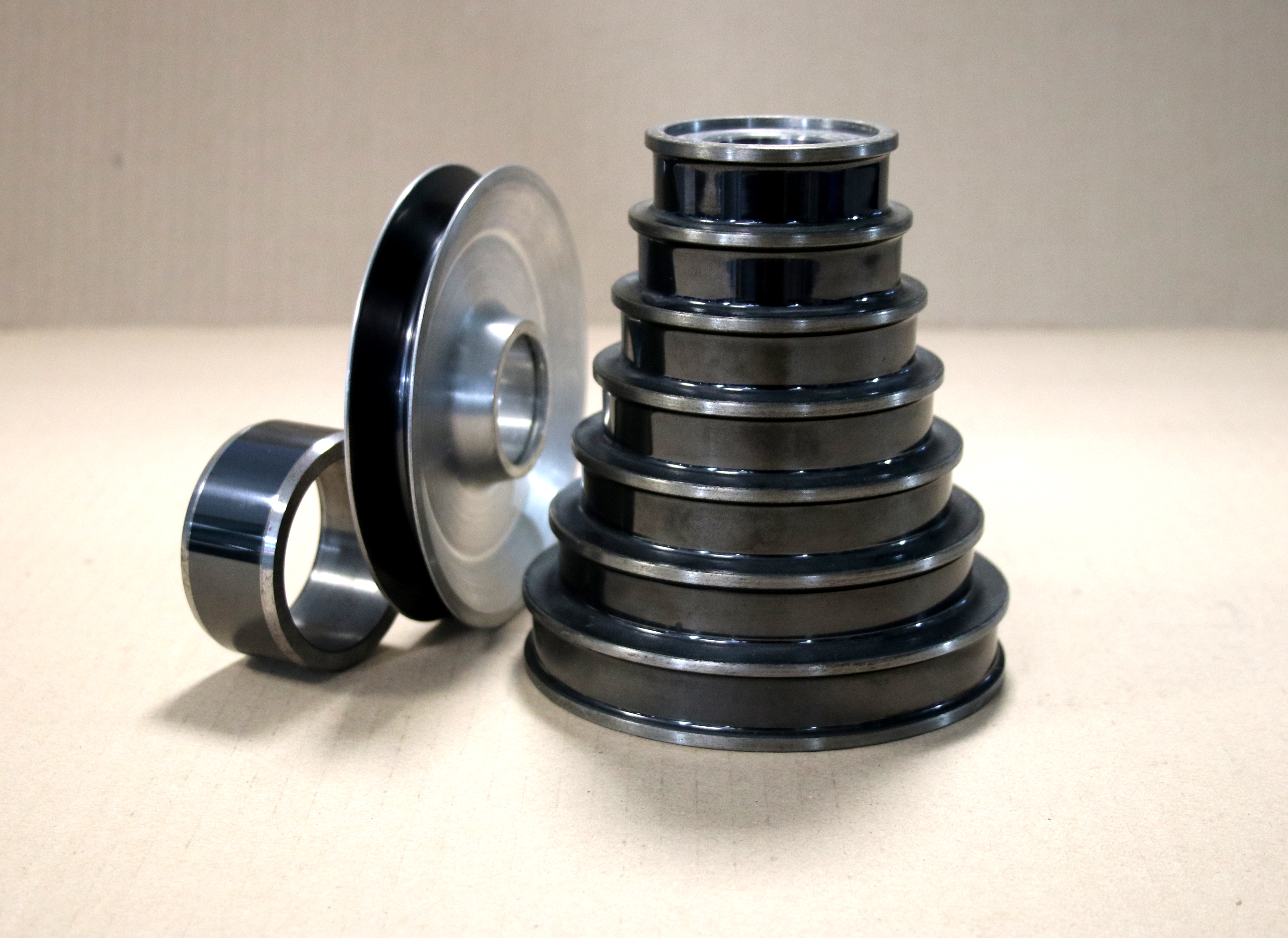
The transition to chromium carbides
To overcome the limitations of tungsten coatings, the industry began to explore alternative materials, including chromium carbides. Paganoni’s Kerblack® is an example of an advanced chromium oxide coating designed to offer superior protection against wear and corrosion. Chromium carbides are known for their high resistance to corrosion and seizing, making them ideal for applications in aggressive environments such as dry drawing of ferrous and non-ferrous metals.
Paganoni’s Kerblack® offers a number of advantages over traditional tungsten coatings. First of all, its enhanced corrosion resistance makes it suitable for a wide range of industrial applications, even in aggressive environments. In addition, the chromium carbide coating is designed to reduce the friction coefficient of the wire on the surface of coated parts, thus improving the efficiency and quality of the drawing process.
Coating chrome carbides with Paganoni
Chromium carbides offer a number of advantages over traditional tungsten coatings. First of all, they are characterised by greater corrosion resistance, which makes them suitable for a wide range of industrial applications.
In addition, chromium carbide coatings, such as Paganoni’s Kerblack®, are designed to reduce the coefficient of friction of the wire on the surface of coated parts, thus improving the efficiency and quality of the drawing process.
The evolution of materials for industrial wire drawing has seen a transition from traditional tungsten coatings to more modern chromium carbides. This transition was driven by the need to improve corrosion resistance and optimise the performance of wire drawing machines. Choosing chrome carbides from Paganoni means relying on the latest frontier in the protection of mechanical parts used in industrial wire drawing, with significant advantages in terms of durability, quality and efficiency.