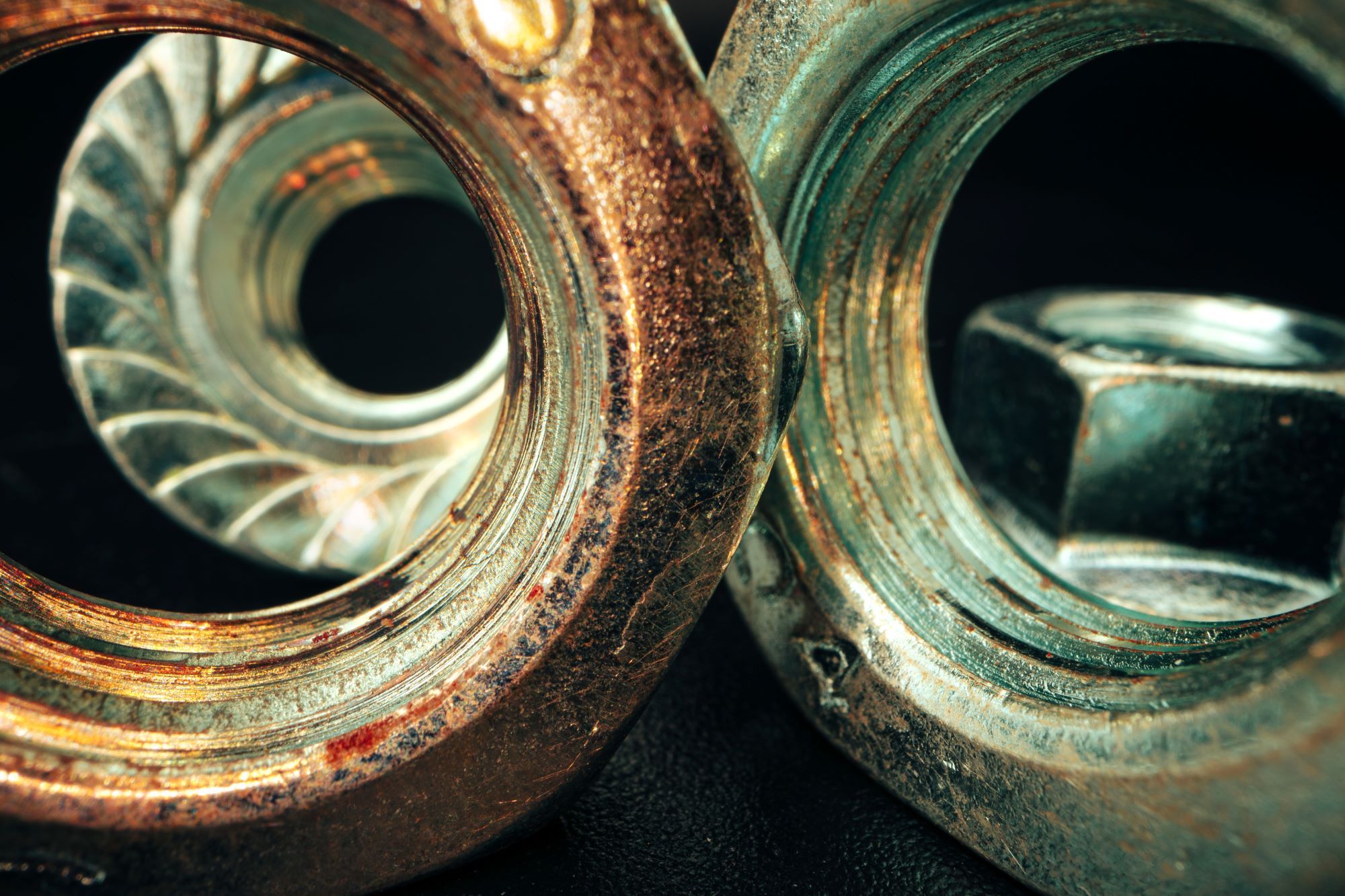
Galvanic corrosion: Challenges and solutions in wire drawing
Galvanic corrosion is an electrochemical phenomenon that occurs when two different metals come into electrical contact in the presence of an electrolyte. This process can cause significant damage, compromising the integrity of materials.
In the wire drawing industry, understanding and managing galvanic corrosion is crucial to maintaining the efficiency of production processes and the quality of end products. This article explores the causes of galvanic corrosion, its specific impact on wire drawing and advanced solutions to prevent it.
What are the causes of Galvanic Corrosion in wire drawing?
Galvanic corrosion occurs mainly due to electrochemical potential differences between two metals. When these metals are connected in the presence of an electrolyte, a galvanic cell is formed in which the metal with the more negative potential (anode) corrodes, while the metal with the more positive potential (cathode) remains protected.
Humidity, temperature and the presence of chemicals in the production environment can accelerate the galvanic corrosion process. Humid environments or environments containing corrosive substances such as salts or acids can increase the electrical conductivity between metals, promoting corrosion.
In wire drawing, various metals and alloys are used. Some materials, such as stainless steel and aluminium, are more susceptible to galvanic corrosion when coupled with other metals. It is essential to select compatible materials to reduce the risk of corrosion.
Galvanic corrosion prevention
The selection of compatible materials is crucial. Using metals with similar electrochemical potentials can significantly reduce the risk of galvanic corrosion. For example, couplings between stainless steel and copper should be avoided.
The use of advanced coatings can protect components from corrosion.
Products such as Paganoni’s Kerblack® coating offer superior protection by creating a barrier that prevents direct contact between dissimilar metals and the electrolyte. Kerblack® is particularly effective in dry drawing, where the absence of lubricants increases the risk of corrosion.
Design strategies may include the use of electrical insulators to separate incompatible metals. In addition, designing components to avoid moisture stagnation or corrosion build-up can reduce the risk of corrosion.
Treatments, maintenance and repair
Applying surface treatments, such as passivation or plating, can improve the corrosion resistance of metal components. These treatments form a protective layer on the metal surface, reducing its reactivity.
Regular maintenance is essential to identify and mitigate early signs of corrosion. Regular inspections and cleaning of components can prevent deterioration. In wire drawing, monitoring material wear and replacing damaged parts in a timely manner is crucial.
When galvanic corrosion occurs, repair techniques such as replacing corroded components or applying protective coatings can be used. Paganoni offers advanced solutions for component recovery, including coating treatments with resistant materials such as Kersint®, which can be used in both dry and wet drawing.
Managing galvanic corrosion, future perspectives and Paganoni solutions
The wire drawing industry continues to evolve with new technologies and emerging materials to combat galvanic corrosion.
Innovative solutions such as advanced coatings and surface treatments are improving the durability and reliability of metal components.
Paganoni is at the forefront of the development of corrosion-resistant materials such as Kersint®. These materials offer advanced protection, improving component life and reducing maintenance costs. With an ongoing commitment to innovation, Paganoni continues to provide effective solutions to address the challenges of galvanic corrosion in the wire drawing industry.
With the adoption of advanced materials and the implementation of intelligent design strategies, the impact of galvanic corrosion can be significantly reduced, ensuring greater efficiency and sustainability of drawing processes.