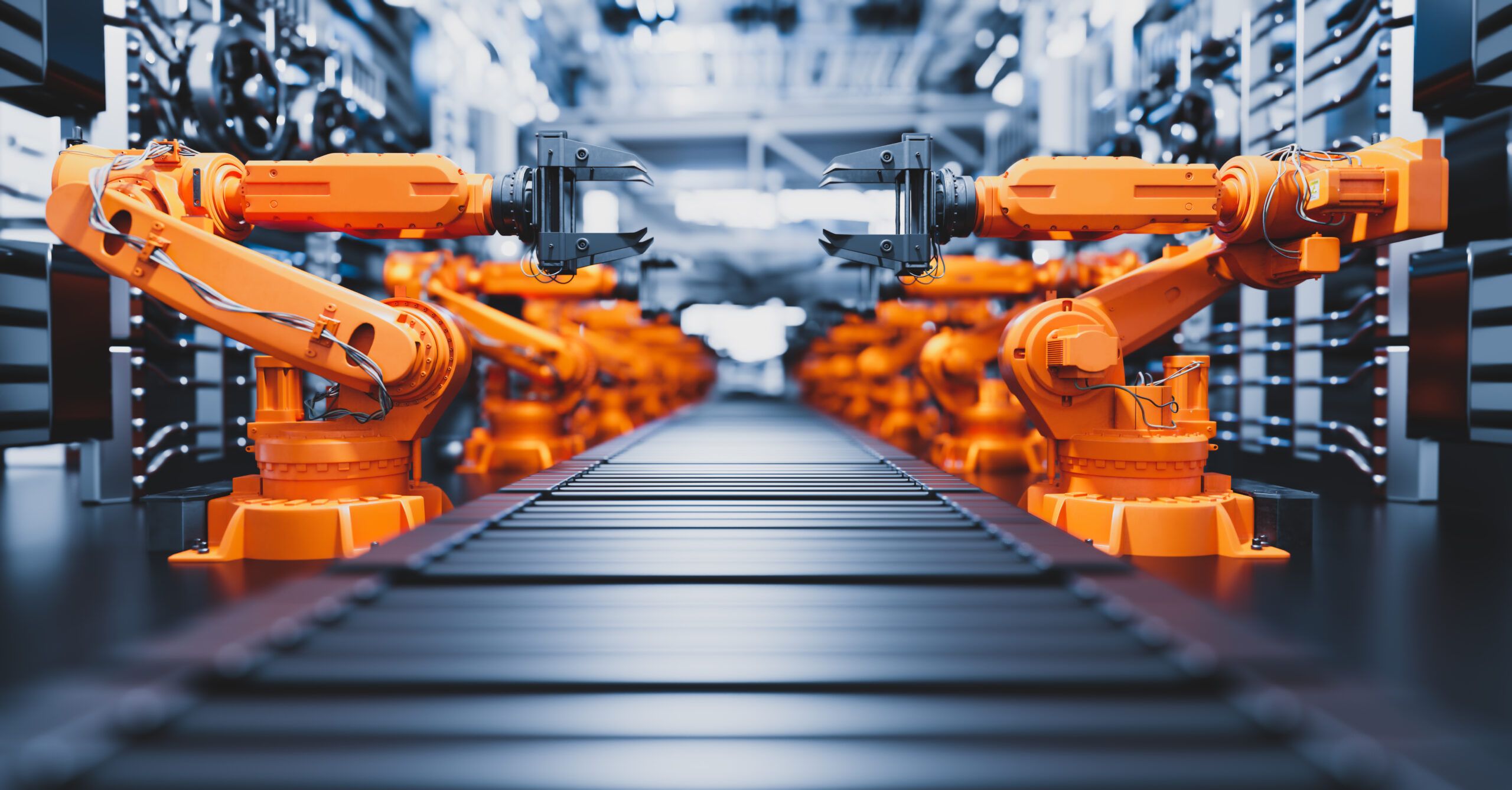
Digitalisation in the wire-drawing industry: IoT, Artificial Intelligence and Big Data
In the age of digitalisation, the wire drawing industry is increasingly embracing emerging technologies to improve operational efficiency and optimise production processes. In particular, a crucial role is being played by the Internet of Things (IoT), along with artificial intelligence (AI) and big data analysis in the wire drawing industry.
How are these technologies revolutionising wire drawing operations? We delve into how they can enable greater precision, better maintenance and more efficient use of resources.
Internet of Things and applications in wire drawing
The digital transformation of the wire drawing industry is enabled by the Internet of Things (IoT), an interconnected network of devices and machinery equipped with sensors and advanced technologies. These devices, an integral part of the so-called Industrial Internet of Things (IIoT), enable the transmission and reception of critical data, thereby improving the monitoring and optimization of wire drawing operations. IoT in industry, often referred to as Industry 4.0, is rapidly becoming a key pillar for improving efficiency and productivity in the wire drawing industry.
In industrial wire drawing, this technology enables real-time connection and monitoring of machinery and equipment. Smart sensors embedded in drawing equipment collect crucial data on machine performance, temperature, pressure and more. This data is then transmitted and analyzed via an IoT network, enabling operators to monitor operations and detect any impending anomalies or failures in a timely manner.
In addition, the IoT facilitates preventive maintenance, allowing operators to schedule maintenance work based on the collected diagnostic data, thereby reducing downtime and optimizing overall productivity.
Artificial intelligence and product quality prediction
Artificial intelligence plays a key role in wire drawing, especially in predicting product quality. Using machine learning algorithms, AI analyzes historical and real-time data to develop advanced predictive models that identify optimal process parameters to ensure maximum final yield.
These models also enable the detection of anomalies or potential defects during the production process, allowing operators to take prompt action to avoid rejects or nonconforming products. In addition, artificial intelligence continuously optimizes process parameters based on past performance and current environmental conditions, ensuring efficient and high-quality production.
> Read also: Dimensional Control: A Key Aspect in Producing Complex Geometries
Big data analytics to optimize production
Big data analytics is revolutionizing the drawing industry by enabling meaningful insights to be extracted from the vast amount of data generated during production operations. Using advanced data analysis tools, companies can identify hidden trends, correlations and patterns in wire drawing data, enabling a better understanding of process dynamics and machine performance.
This in-depth knowledge enables operators to optimize process parameters, reduce waste and improve overall production efficiency. In addition, big data analysis supports informed maintenance decisions, enabling proactive equipment management and reduced maintenance costs.
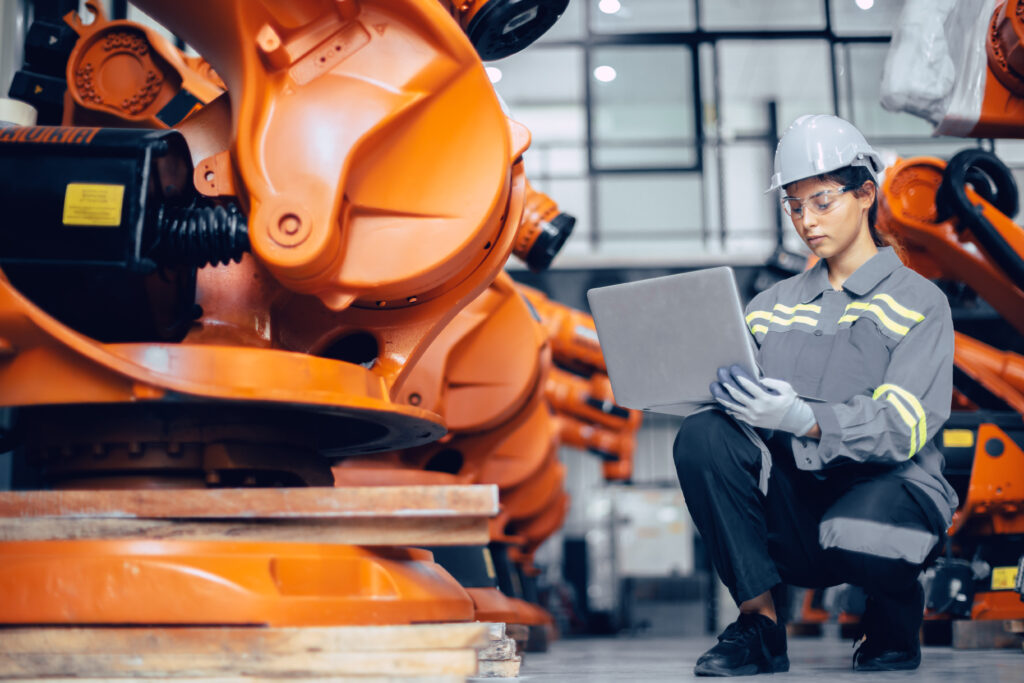
Looking to the future, the wire drawing industry is preparing to take full advantage of the opportunities offered by digitalization, leading the industry to new frontiers of innovation and growth.
Paganoni, with its extensive experience in the wire drawing industry, is leading the way in adopting digital technologies to optimize production operations, becoming an essential catalyst for competitiveness in the industry.