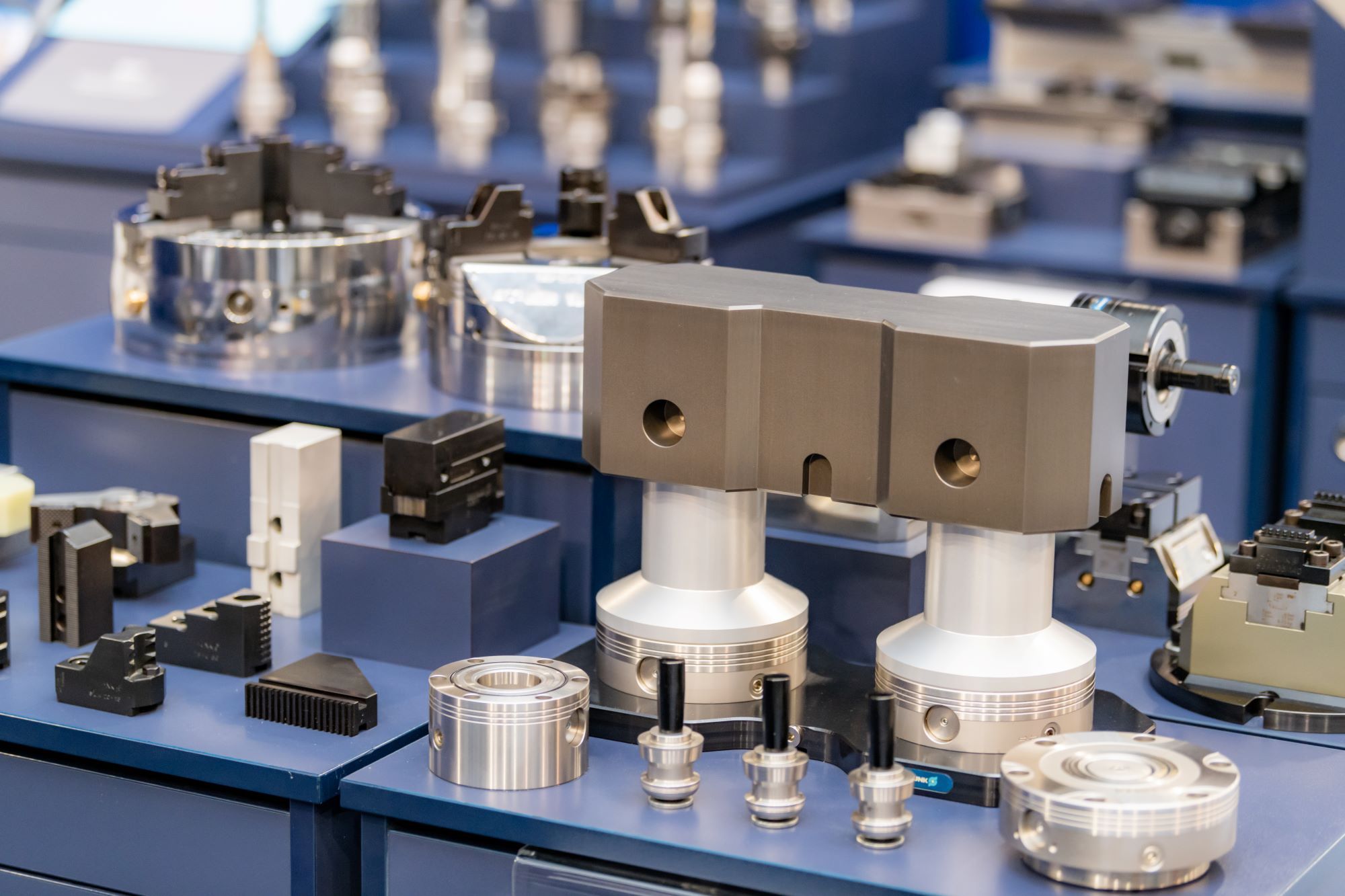
Innovative applications of wire drawing, among Automotive, Precision Electronics and Biomedicine
The wire-drawing process, which consists of reducing the cross-section of a wire, tube or bar through a die, is experiencing an unprecedented phase of innovation.
This technology, which has been used for decades, is evolving to meet the needs of various industries, including automotive, electronics and biomedical.
New applications of wire drawing not only improve production efficiency but also the performance and quality of finished products. In this article, we will explore the new applications of wire drawing in these three key sectors.
Advanced Wire Drawing for the Automotive Industry
The automotive industry is constantly evolving, driven by the need to create more efficient, safe and sustainable vehicles. Wire drawing plays a crucial role in the production of automotive components, especially for electric and autonomous vehicles.
- Light and Strong Components
Reducing the weight of vehicles is a priority to improve fuel efficiency and reduce emissions. Drawing allows the production of lightweight yet extremely strong automotive components. Materials such as aluminium and titanium alloys, precisely drawn, are used to make chassis, suspension systems and other critical vehicle parts.
- Energy Efficiency in Electric Vehicles
In electric vehicles, efficient energy management is crucial. Wire drawing enables the production of conductive wires and cables with optimal properties, improving the efficiency of electric motors and power systems. Advanced coatings such as those developed by Paganoni, e.g. Wolside® and Kerblack®, offer wear resistance and optimal conduction, essential for the high performance required by electric vehicles.
- Autonomous Vehicles
Autonomous vehicles require advanced sensors and reliable connection systems. Precision wire drawing is used to produce critical components such as connectors and sensor wires, which must be highly reliable and durable. Wire drawing technologies enable smooth surfaces and precise dimensions, which are essential for the safe operation of autonomous systems.
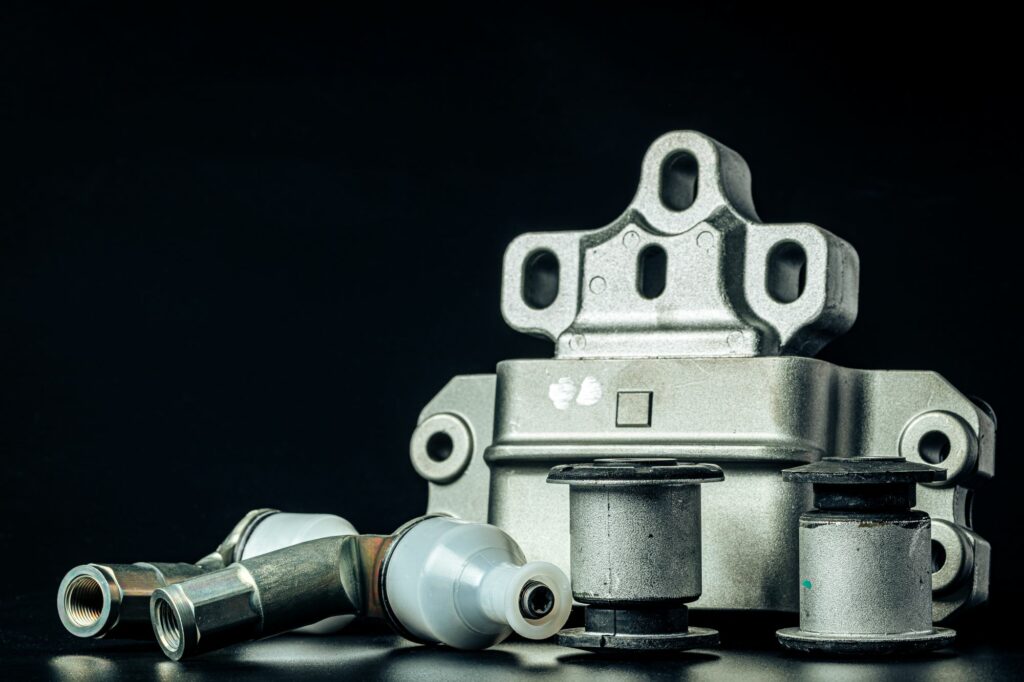
Wire drawing technologies for precision electronics
Precision electronics require smaller components with high reliability and superior performance. Wire drawing is crucial in the production of such components, ensuring tight tolerances and exceptional surface finishes.
- Electrical contacts and connectors
Electrical contacts and connectors are critical components in electronic devices, from computers to medical devices. Wire drawing allows wires and cables to be produced with optimal conductivity and mechanical strength. Coatings such as Niksint®, developed by Paganoni, offer corrosion and wear resistance, extending the life of the components.
- Components for medical devices
The miniaturisation of medical devices requires extremely precise electronic components. Wire drawing produces thin, robust wires used in pacemakers, insulin pumps and other wearable technologies. Precision wire drawing ensures that these components function reliably in critical environments.
- Wearable technologies
Wearable devices, such as smartwatches and fitness trackers, require lightweight and flexible electronic components. Wire drawing enables the production of wires and micro-components with the necessary mechanical properties to be integrated into flexible fabrics and materials. These components must withstand constant bending and wear, while ensuring high performance.
> Read also: Seeking innovation: Market trends in the wire drawing industry
Drawing Applications for the Biomedical Industry
The biomedical sector presents unique challenges for wire drawing, with stringent requirements in terms of biocompatibility, precision and strength.
- Medical Devices
As with electronic components for certain devices, wire drawing is essential in the production of medical devices such as stents, catheter guides and hypodermic needles. These devices require a combination of flexibility and strength, achieved through advanced drawing processes. Materials such as stainless steel and cobalt-chromium alloys are commonly drawn for these applications.
- Prosthetics
The production of prostheses requires materials that are light but also extremely strong. The drawing of titanium alloys and other biocompatible materials makes it possible to create prosthesis components that are durable and safe for long-term use in the human body. The precision of the drawing ensures that these prostheses fit the patient perfectly, improving quality of life.
- Surgical Instruments
Surgical instruments must be incredibly precise and corrosion-resistant. The drawing of stainless steels and special alloys makes it possible to produce scalpels, scissors and other surgical instruments with sharp edges and smooth surfaces. Corrosion resistance is crucial to ensure sterility and durability of instruments.
Amidst endless innovation, a multi-sector future of wire drawing
Innovative applications of wire drawing are transforming various industries, from automotive to electronics to biomedical. Companies like Paganoni are at the forefront of this evolution, offering advanced products such as Wolside®, Kerblack®, Coldside® and Niksint®, which improve the efficiency, quality and sustainability of wire drawing processes.
With the continuous adoption of new technologies and materials, wire drawing will continue to play a crucial role in industrial and technological progress.