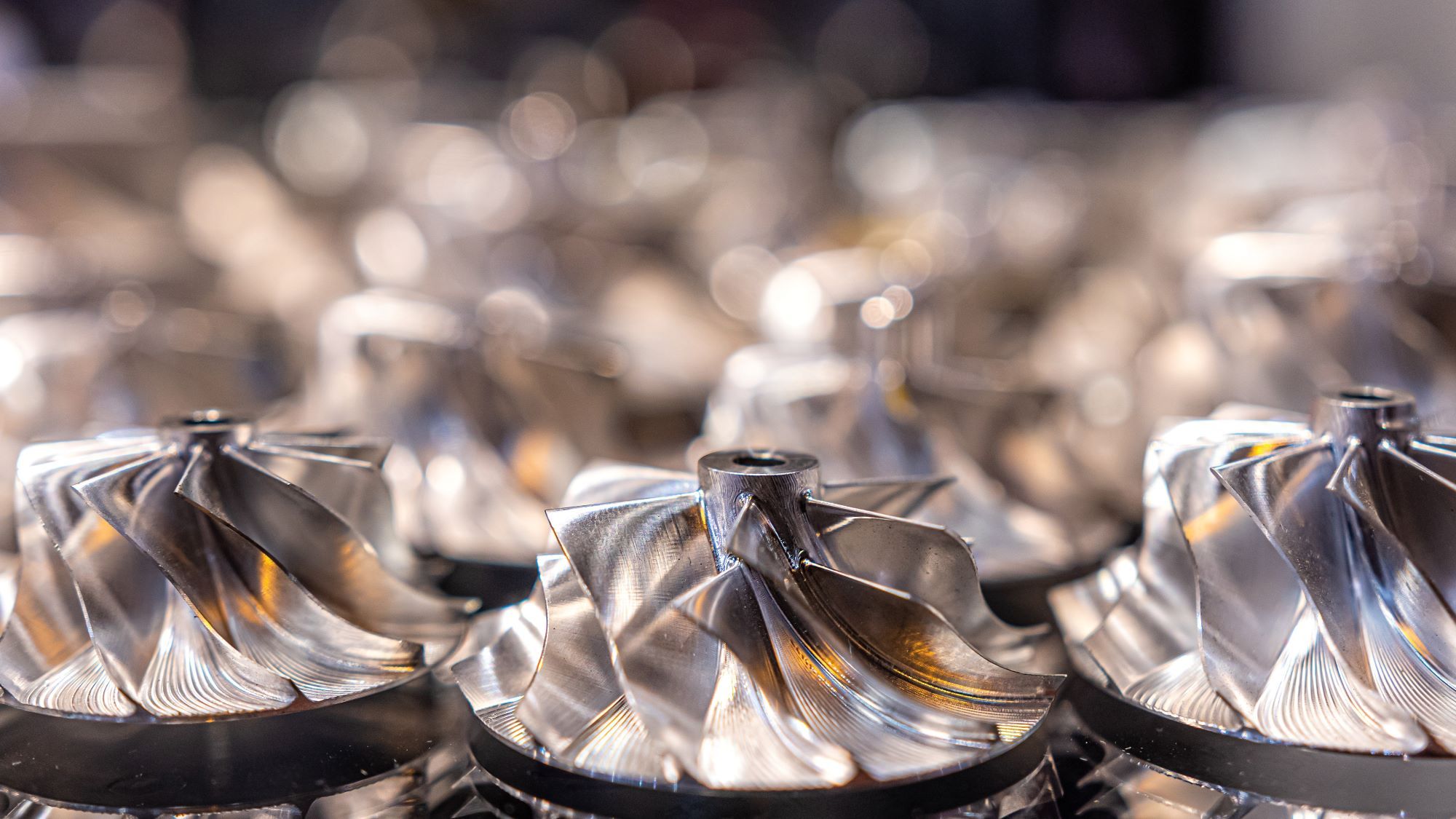
Tungsten melting point: The effects on Coating Processes
Tungsten is one of the most widely used materials in industry due to its incredible resistance to high temperatures and mechanical stress. This metal has the highest melting point among pure elements, reaching 3,422°C, well above most industrial materials. This property makes tungsten particularly suitable for applications requiring resistance under extreme conditions, including advanced coating processes. However, it is precisely its high melting point that presents a challenge in industrial machining and processing, requiring sophisticated technologies that can handle the heat without compromising the physical properties of the coatings and substrate.
In this context, the Paganoni company stands out for its innovative solutions proposed for tungsten carbide coatings, ideal for guaranteeing durability and excellent performance in difficult operating conditions, such as those found in metal drawing.
Applications of tungsten in coating processes
The use of tungsten for coatings begins with its transformation into tungsten carbide, a form that, when applied to components, creates an extremely hard and resistant protective layer. Coldside®, the material developed by Paganoni based on tungsten carbide, is an example of how tungsten can be processed to improve the efficiency of drawing processes by providing a highly resistant barrier to wear and corrosion.
Tungsten carbide coating in wire drawing is often used on capstans, pulleys and other mechanical components to increase their service life and reduce the need for maintenance.
Due to the stability and hardness of tungsten, coated components maintain high performance even under demanding working conditions, such as in wire drawing processes where surfaces must withstand continuous contact with metals and alloys.
Benefits of tungsten in industrial coatings
Tungsten coatings, such as those offered by Paganoni, offer countless benefits:
- Extreme wear resistance: Tungsten carbide provides high durability and protects components from abrasion, ideal for applications such as wire drawing. Paganoni’s Coldside® coatings, for example, are specially designed to preserve the surfaces of capstans and pulleys, helping to reduce maintenance costs and extend the life of machinery.
- Heat resistance: Tungsten-based coatings can withstand very high temperatures without degrading. This property is particularly useful in high-temperature industries such as aerospace and engineering.
- Corrosion protection: Tungsten carbide forms an effective barrier against corrosive agents, reducing the risk of oxidation and protecting components even in chemically aggressive environments. Paganoni offers specific coatings that meet the needs of the most demanding sectors, where chemical resistance is essential.
- Friction reduction: Tungsten coatings can reduce the friction coefficient, improving the energy efficiency of industrial processes. Thanks to this characteristic, coated components, such as those developed by Paganoni, optimise performance and reduce mechanical stress.
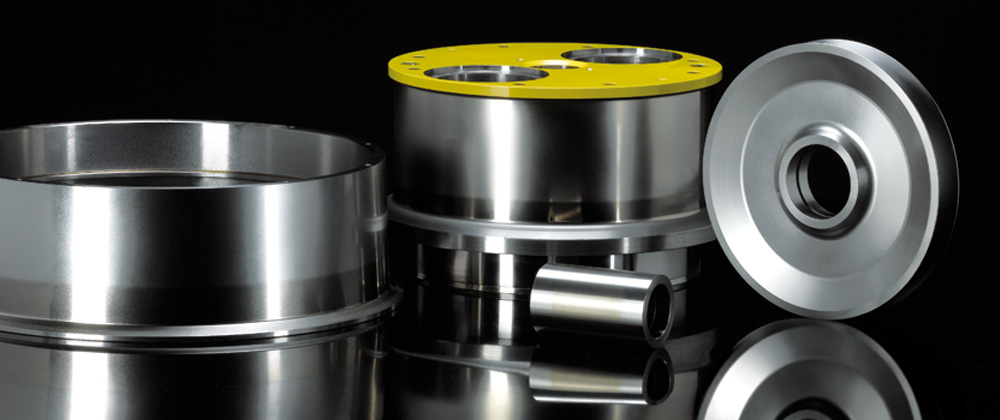
Operational challenges and limitations of tungsten
Despite its many advantages, tungsten presents operational challenges, mainly related to its high melting point and high costs.
- High temperatures: machining tungsten requires advanced equipment and specific technologies to handle the heat. Paganoni, for example, specialises in the use of advanced techniques such as HVOF, which allows tungsten to be used even in areas where intense heat is a limiting factor.
- Fragility: Pure tungsten is inherently brittle, which is why it is often combined with other elements to achieve the required hardness and strength. However, this requires specific skills and state-of-the-art handling technology, such as that used by Paganoni.
- Production costs: Tungsten is an expensive material, but the cost is largely repaid by the high durability and performance of the coatings. However, companies must carefully weigh up the costs and benefits to gain a real competitive advantage.
Tungsten in advanced industrial coatings with Paganoni’s solutions
Tungsten remains a key material for the industrial coatings industry due to its high resistance to heat and hardness. Paganoni ‘s advanced solutions demonstrate the effectiveness of tungsten carbide coatings in critical environments such as wire drawing, where surfaces are subject to wear and thermal stress.
With Coldside® coatings and other technical innovations, Paganoni helps to improve the performance of industrial components, reducing maintenance costs and ensuring a high degree of protection against corrosion and wear.These coatings not only extend the life of components, but also optimise industrial processes, positioning tungsten as a benchmark material for quality and long-term reliability.