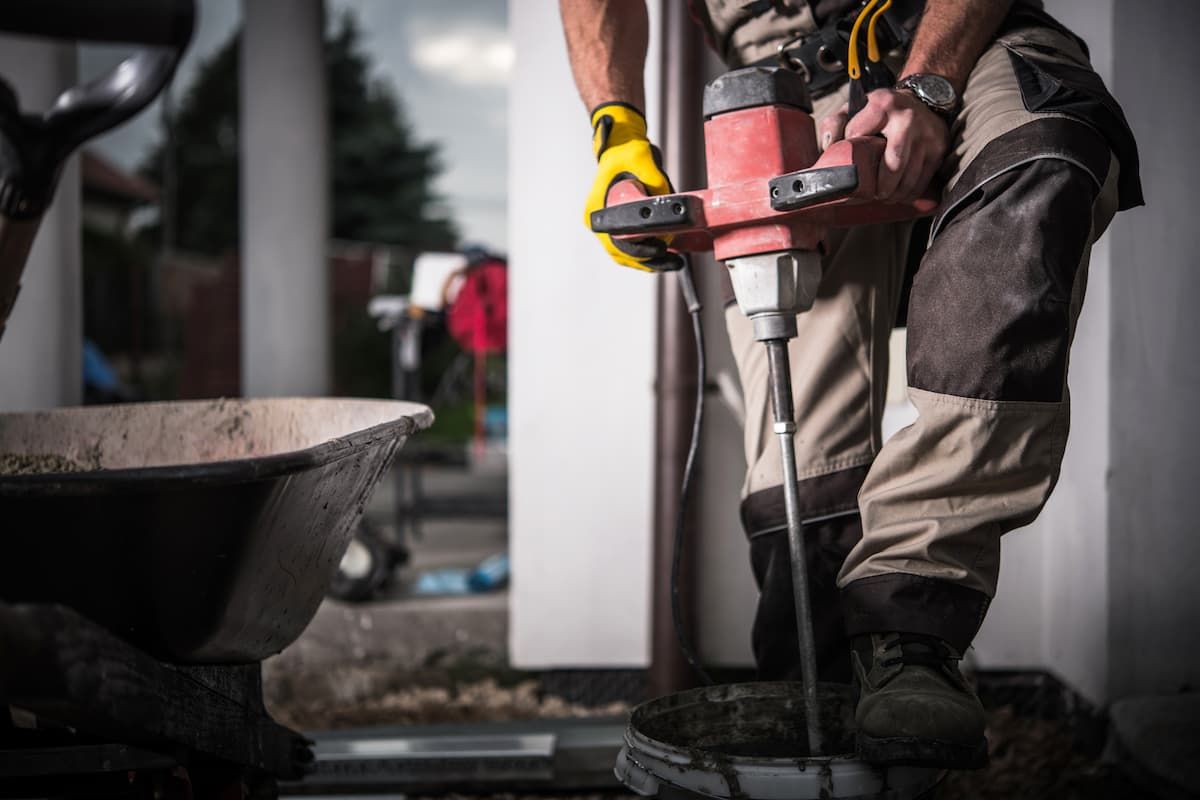
Tungsten Melting: Technologies, Applications, and Challenges
Tungsten, also known as wolfram, is an element of crucial importance in numerous industrial sectors. Its extraordinarily high melting point, about 3422°C, makes it unique but also challenging to work with, requiring advanced melting techniques and specific methodologies.
Tungsten is a dense and hard metal, with high tensile strength. It is also corrosion-resistant and has low thermal expansion, which means it maintains its shape and size even when exposed to high temperatures.
These properties, together with its high melting point, make it a valuable material for various industrial uses, from the production of filaments for incandescent lamps to components for electronic devices and the aerospace industry.
READ ALSO: Corrosion Protection in the Aerospace Sector
Melting Points and Techniques
Due to its high melting point, tungsten requires specialized melting methods, such as induction melting. This technique allows reaching and controlling extremely high temperatures, essential for working with such a demanding metal.
Aerospace Sector
In the aerospace sector, molten tungsten is particularly valued for its resistance to high temperatures and corrosion. It is used to produce components for jet engines and other devices that must withstand extreme environmental conditions.
Other Industrial Applications
Besides the aerospace industry, molten tungsten is widely used in various sectors, including electronics and heavy industry. Its exceptional conductivity and resistance properties make it an ideal material for applications requiring robustness and durability over time. An important application of tungsten in these sectors is in the restoration of worn or damaged component geometries.
In restoring geometries, tungsten is often used to rebuild or reinforce parts of machinery or electronic components that have undergone wear, corrosion, or damage. This process is particularly useful in industrial environments where components are subjected to extreme conditions, such as high temperatures or pressures, and where maintenance and longevity of materials are crucial.
Thanks to its hardness and heat resistance, tungsten is able to effectively restore the original geometries of these components, significantly extending their useful life and improving their operational efficiency.
Tungsten Melting Methods
The melting process of tungsten employs cutting-edge technologies. Methods such as electric arc furnace melting and vacuum techniques are fundamental to meet the specific needs of this metal.
READ ALSO: Precision Mechanical Parts: When Perfection is a Requirement
Properties of Molten Tungsten
Molten tungsten offers significant benefits, such as high density, resistance to extreme temperatures, and excellent conductivity properties, making it an ideal material for applications in challenging conditions.
The melting of tungsten poses considerable challenges. The process requires advanced and expensive equipment, and the metal itself, due to its hardness and brittleness at lower temperatures, requires precise handling.
In summary, the melting of tungsten is a complex but vital process in various industrial and aerospace applications. Advanced technologies and specialized techniques have allowed the exploitation of the extraordinary properties of this metal, paving the way for new innovations and technological advancements.